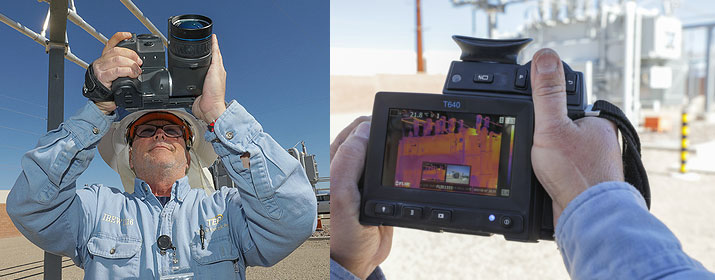
Every summer when temperatures ramp up and energy loads are at their highest, UniSource substation journeymen sweep over specific equipment using a handheld device. They’re looking for “hot spots” using an infrared (IR) thermal imaging camera to identify problem areas before they fail.
“Hot spots are areas most likely to fail, causing unplanned outages,” said UniSource Substation/Relay/Communication Supervisor John Steele. “The hottest spots show up as bright white, while the areas around it may be deep orange, purple or red. The lighter white areas are conducting poorly, causing conductive material to heat up.”
Failure of just one critical piece of equipment in a substation can result in a widespread outage, delayed restoration time and costly repairs in addition inconveniencing our customers. Using IR technology as a preventative measure helps us catch failures before they occur, which saves resources to help reduce our operating costs.
“IR technology has been around since the 1960s, but has improved greatly with smaller cameras, more features and clearer images,” said David Gonzalez, Transmission & Distribution Maintenance Engineer.
Like most other utilities, UniSource uses IR technology to evaluate the temperature of equipment compared with the surrounding temperature and is useful for finding abnormal hot spots, loose connections and overloaded conductors. Trained journeymen point the camera’s cross hairs at suspect equipment, such as capacitors, switches and jumper connections, to get a visual temperature reading.
For our Mohave operations, journeyman perform IR scans of all our substations and underground feeder cables every summer and when new installations are commissioned. Anytime temperatures greater than 70 degrees above the ambient temperature are found, a report is submitted to engineering and evaluated. Repairs are scheduled based on severity and impact on our system.
Engineers consider the amount of load on the equipment, its impact on service reliability, age and other factors to determine its risk level and whether replacement is needed and how soon.
Journeymen last year prevented an outage after a hot spot was detected on a distribution switch. During an IR inspection, a journeyman found some come contacts had actually melted from the heat. Engineers ordered immediate repairs.
IR technology is so useful and versatile that we also use it on our transmission lines, poles boxes and underground cables and whenever new equipment, such as a new breaker or transformer, is energized. In winter, it’s also used to monitor equipment heaters, which keep certain equipment dry during cold wet weather when moisture can accumulate from condensation causing rust and electrical tracking.
For a small and relatively affordable piece of equipment, this technology plays a powerful role in preventing larger problems.
“IR inspections are an important preventative maintenance tool,” Gonzalez said. “Performing these scans help us find hot spots and abnormalities before failures occur. Depending on the severity of the temperature deviations, corrective action can be taken to ensure equipment is fully functional for greater reliability.”